It is well known and accepted that, to manage a process, we need to measure the results of that process. If we start measuring the production output of a machine, the people responsible for running and maintaining that machine are more likely to pay attention and take the necessary decisions to improve its performance.
Every business with any focus on continuous improvement has some system that works for them and has evolved as they have traveled their journey. Some use paper, some use paper and spreadsheets, others use custom solutions, and others use some form of off-the-shelf software.
For over 20 years we’ve helped users get the digital data they have into these various systems, but in the process of doing that, we’ve heard some things from them and seen some patterns we will share in this blog post.
Market Demands Increase Need for Scalability in Continuous Improvement
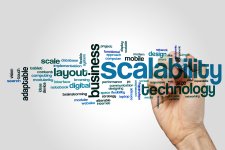
Spreadsheets, a Common Approach
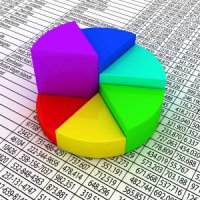
Multi-User Challenges
Accuracy of Data
Auditability
System Breakage
The Multiple Data Source Bowl of Noodles
- Databases
- Other spreadsheets
- Manual data entry
- ERP systems
- Lab systems
- Energy monitoring systems
- Facility management systems
Most conversations we have involve stories of the pain users go through in order to gather up the required data. We’ve even heard of people having to export data from a digital system as a CSV file and then load that into Excel so that they can then relate that data to information they pulled out of a process historian as a CSV file.
A characteristic a solid decision support system should have is the ability to pull data from multiple data sources, and support manual data entry like a spreadsheet, and treat all the data equally.
Cost & Time Realities Often Interfere with Progress
Many companies have big dreams, and big visions, but when they look at their options to move past spreadsheets, they realize the costs to receive any value quickly run into the 10’s or 100’s of thousands of dollars, and they will spend at least 6 months in implementation. With competing demands for capital and staffing challenges due to generational change, they often quickly just decide to deal with the limitations of spreadsheets and keep using them.
A key overall characteristic of a leading Industrial Decision Support system for manufacturers who are ready to move off of spreadsheets is reasonable cost of entry with license prices in the thousands of dollars and time to implement, resulting in time to value, measured in days or weeks, not months.
The Ten Trends
So we’ve talked about some of the key things we’re seeing and hearing. We’ve put together a paper that covers these 10 trends in industrial decision support systems and information portals:
- Systematization
- Promoting Self-Service
- Employing software robots to gather the data
- An understanding that industrial data and business data are different but have to work together
- Automated calculation bridges matter
- Perspective and context without custom code
- Embracing manual data entry
- Seeing and understanding for all
- Encouraging sharing and collaboration
- Enabling the bigger picture